
I played a large part in last development by helping build the 3D modeling process and utilizing tools/ functions to get the outcome we were looking for. We used 3D scans to build our lasts so that each customer has a custom fit. We would then 3D print our lasts out to do traditional pattern making to start building the upper.
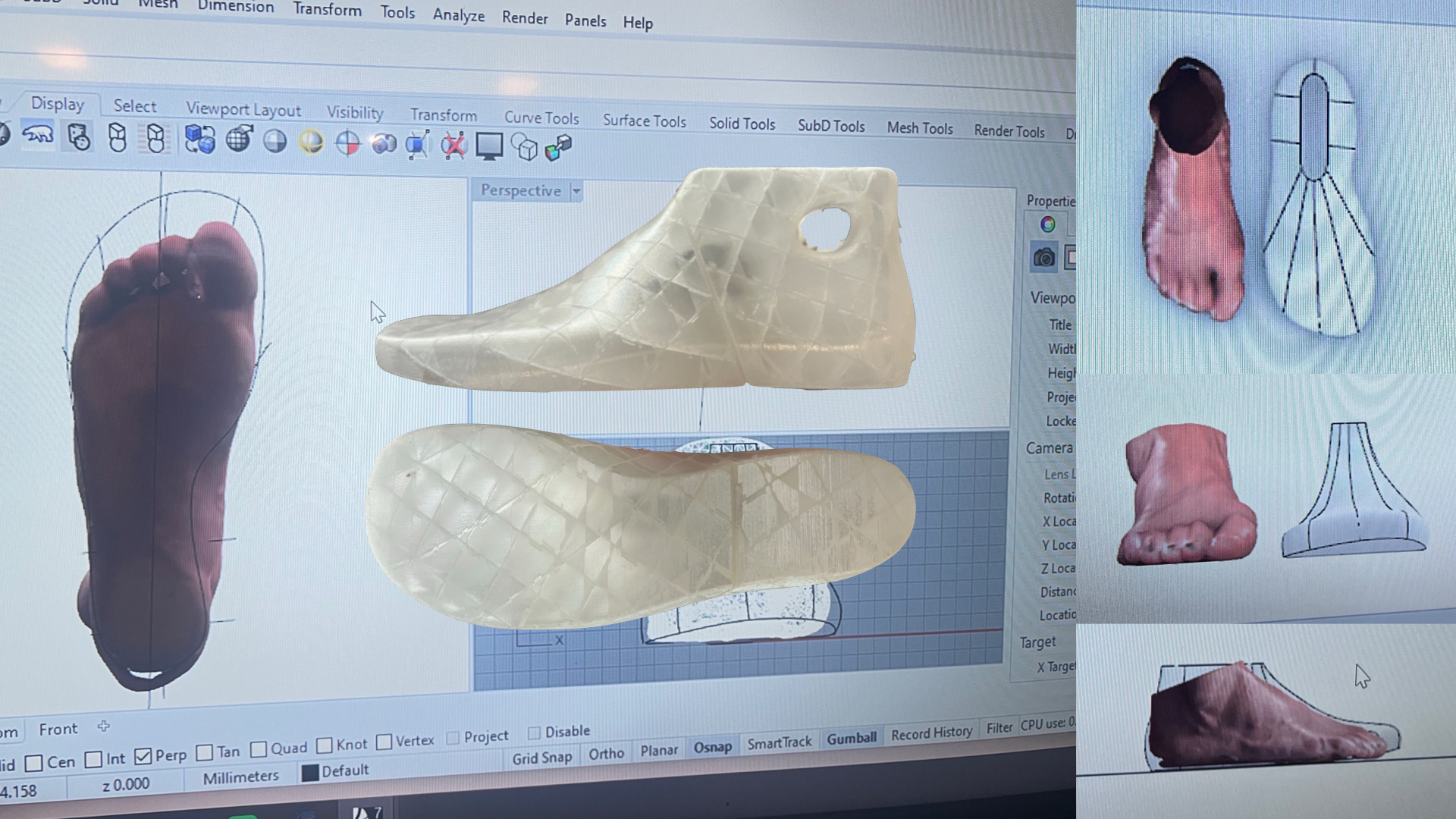
During my time at Code, I influenced design choices and developed a new American football cleat plate. This was a very detail orienting process to get the right flexibility, traction and ergonomic placement. The software I used was Rhino3D where I utilized the displacement to get texture/ patterns.
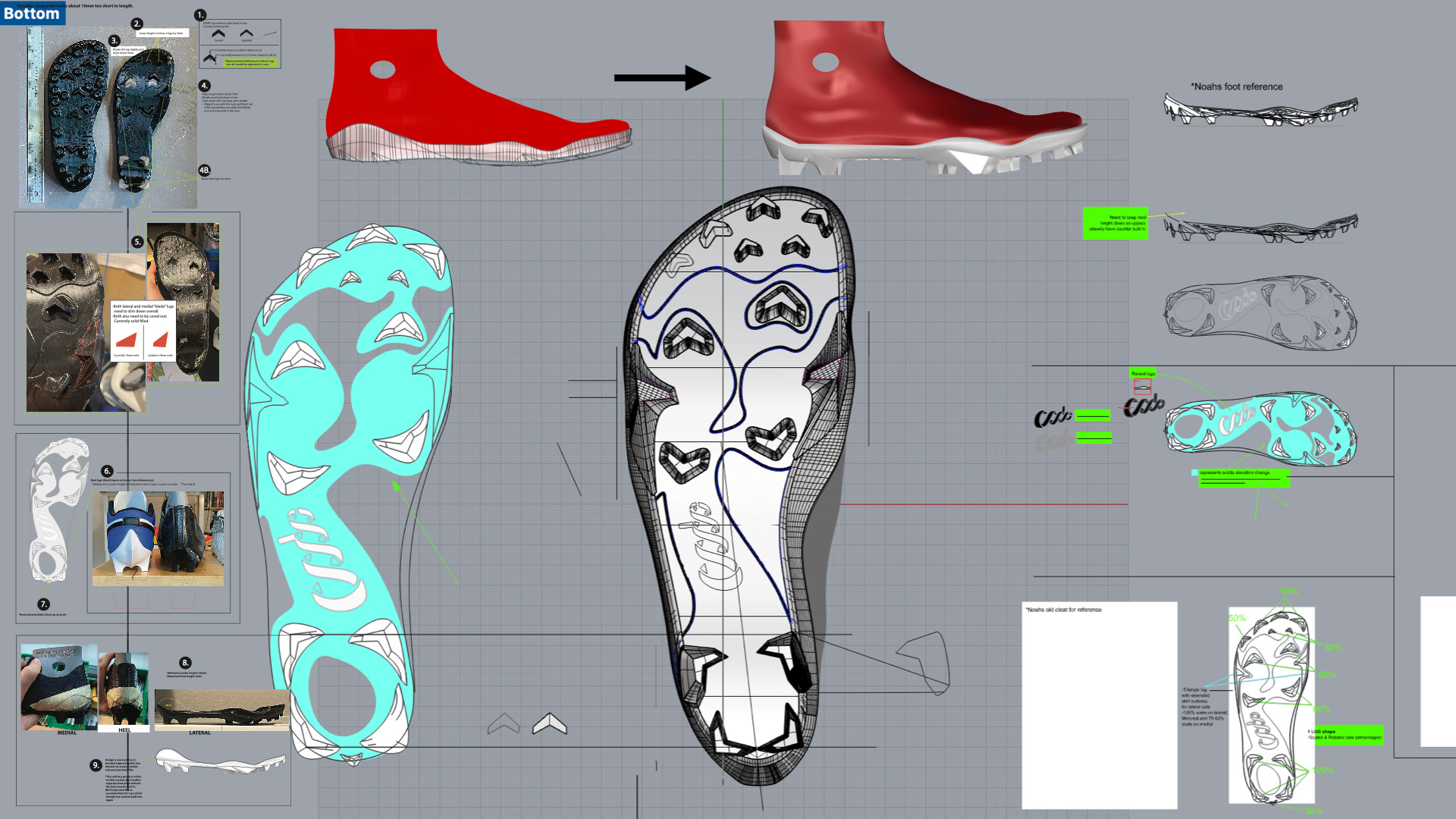
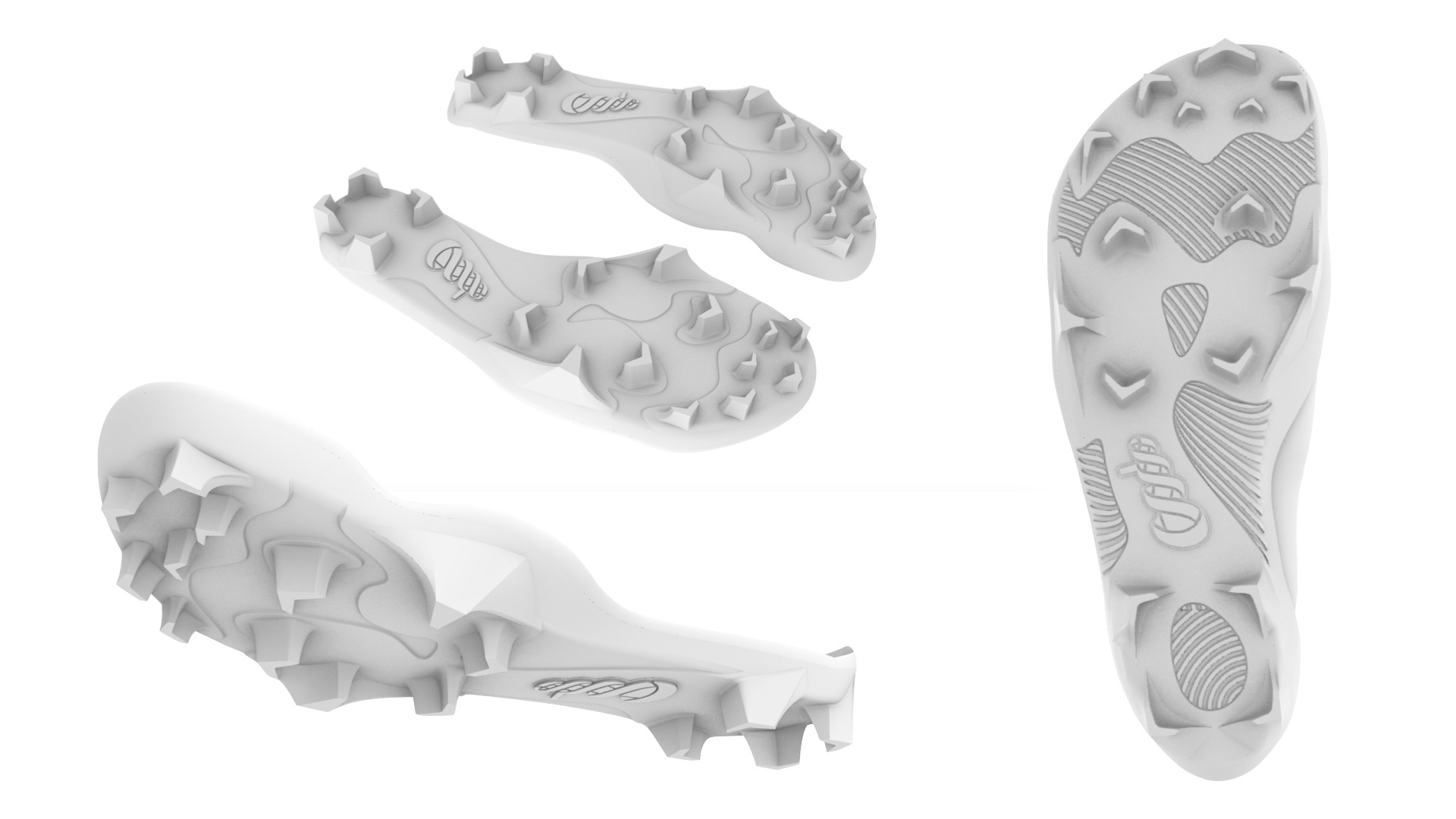
I would help manage and troubleshoot the 3D printers so I became very familiar with fixing problems or errors. It was important to get the best print quality possible so adjusting print settings and properly maintaining the printers were important. After getting a clean print done, we would then assemble the shoe together using a method we found effective for 3D prints.
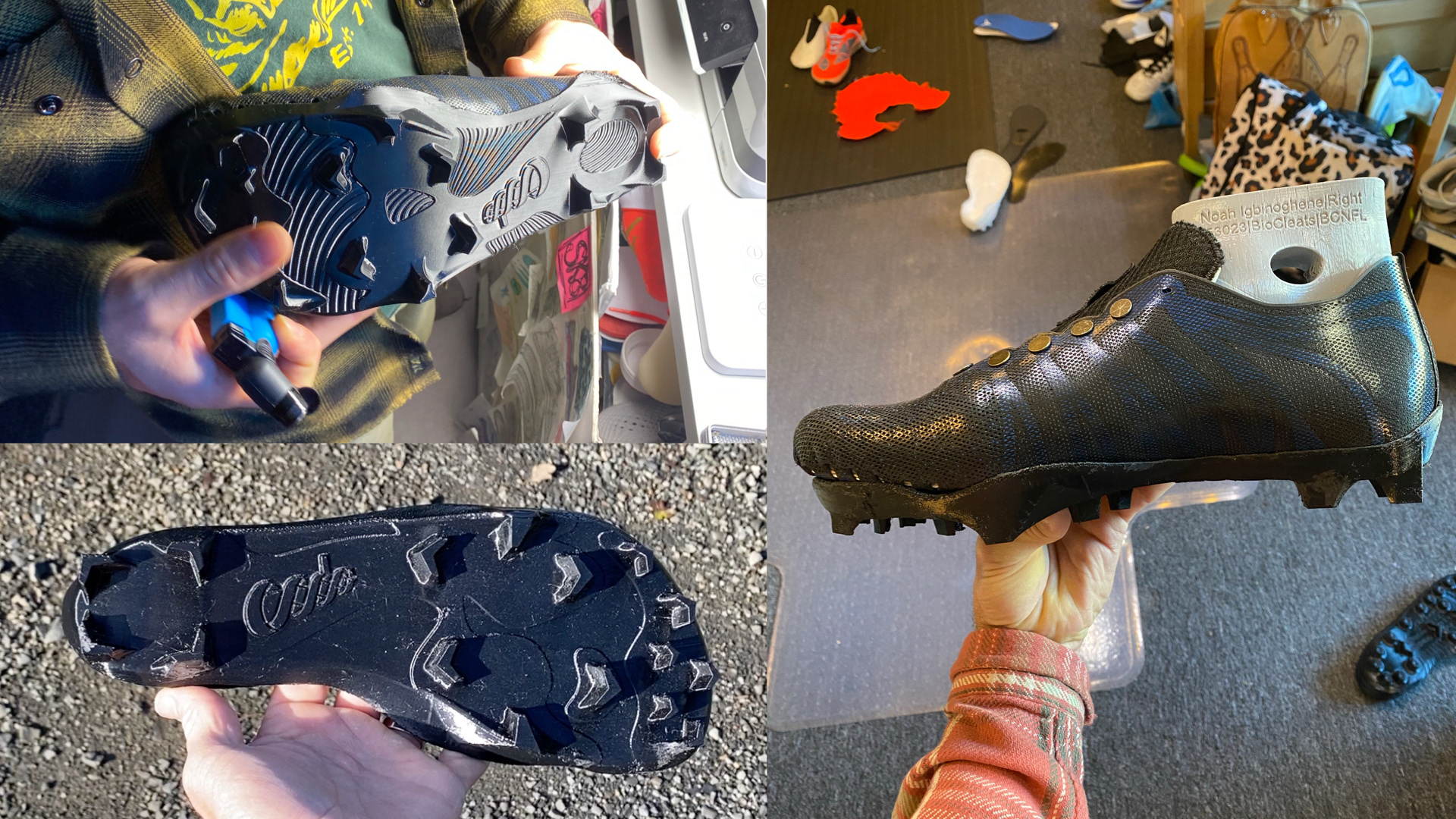
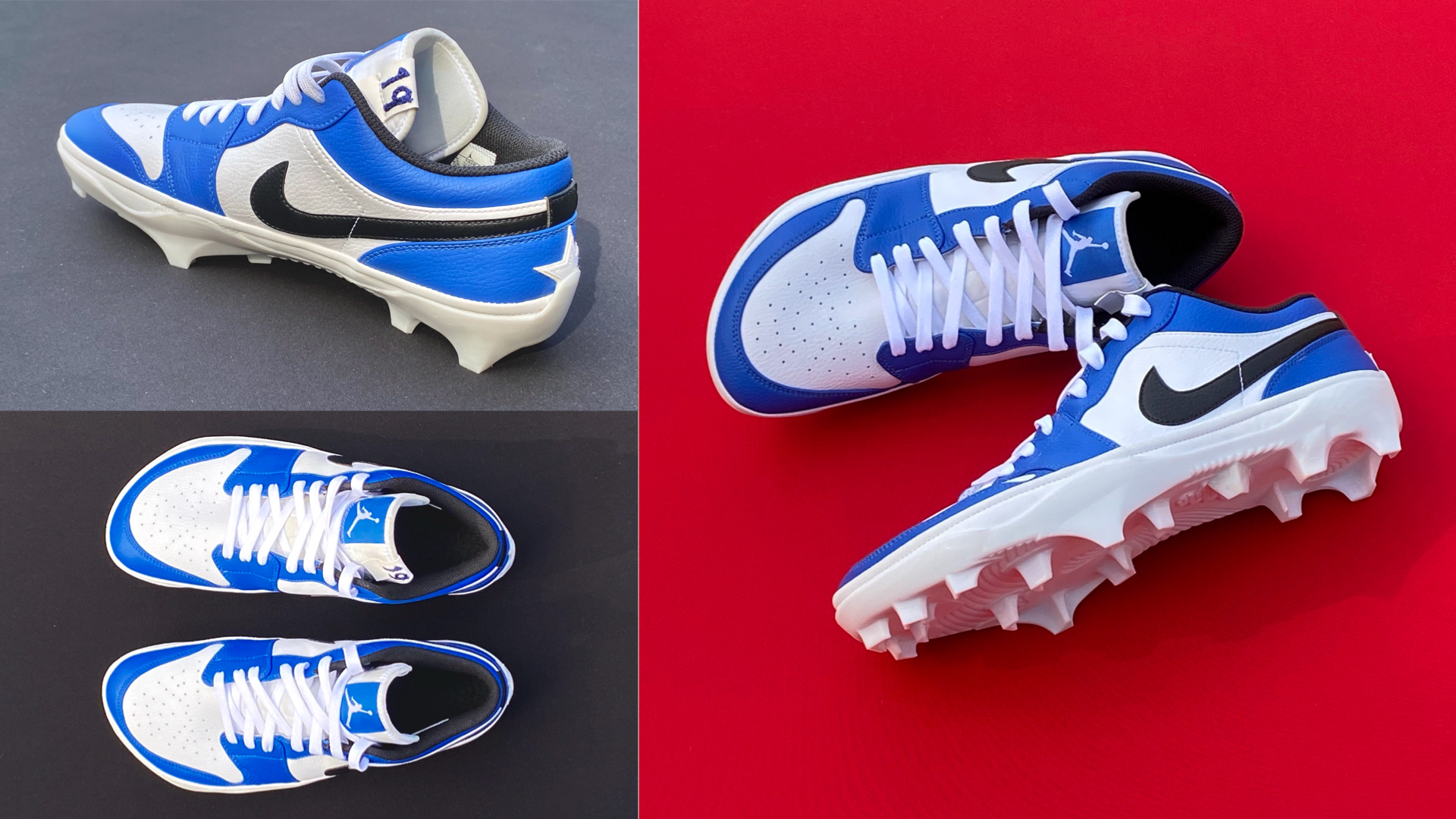
I would also 3D model and print footwear components such as traction samples with different TPU filament durometer and geometry.
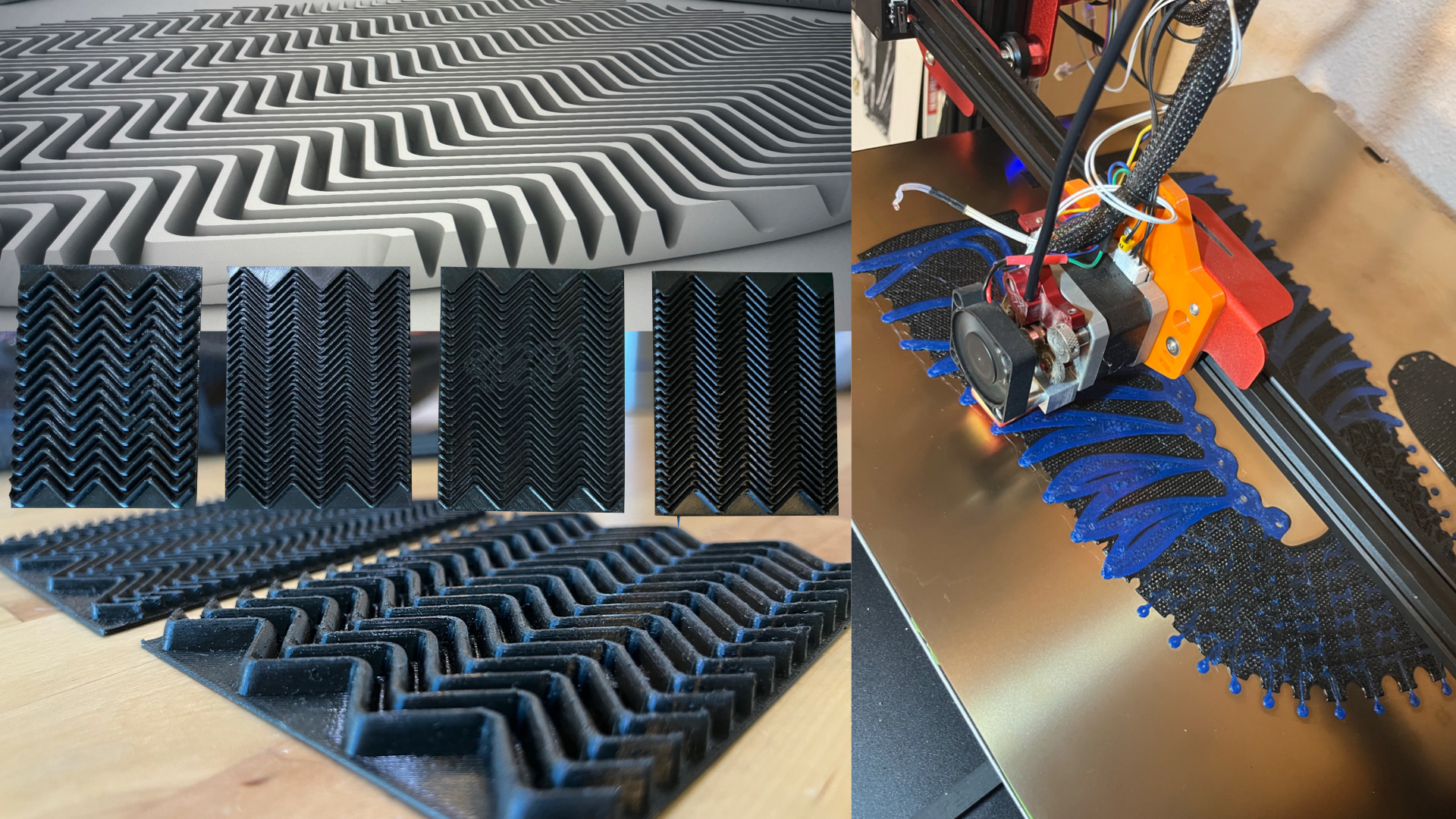
I brought to the table certain construction methods that were found useful to the team and I learned a lot in terms of pattern making and construction. I gained valuable experience in lasting, the art of pattern making and other handy construction methods.
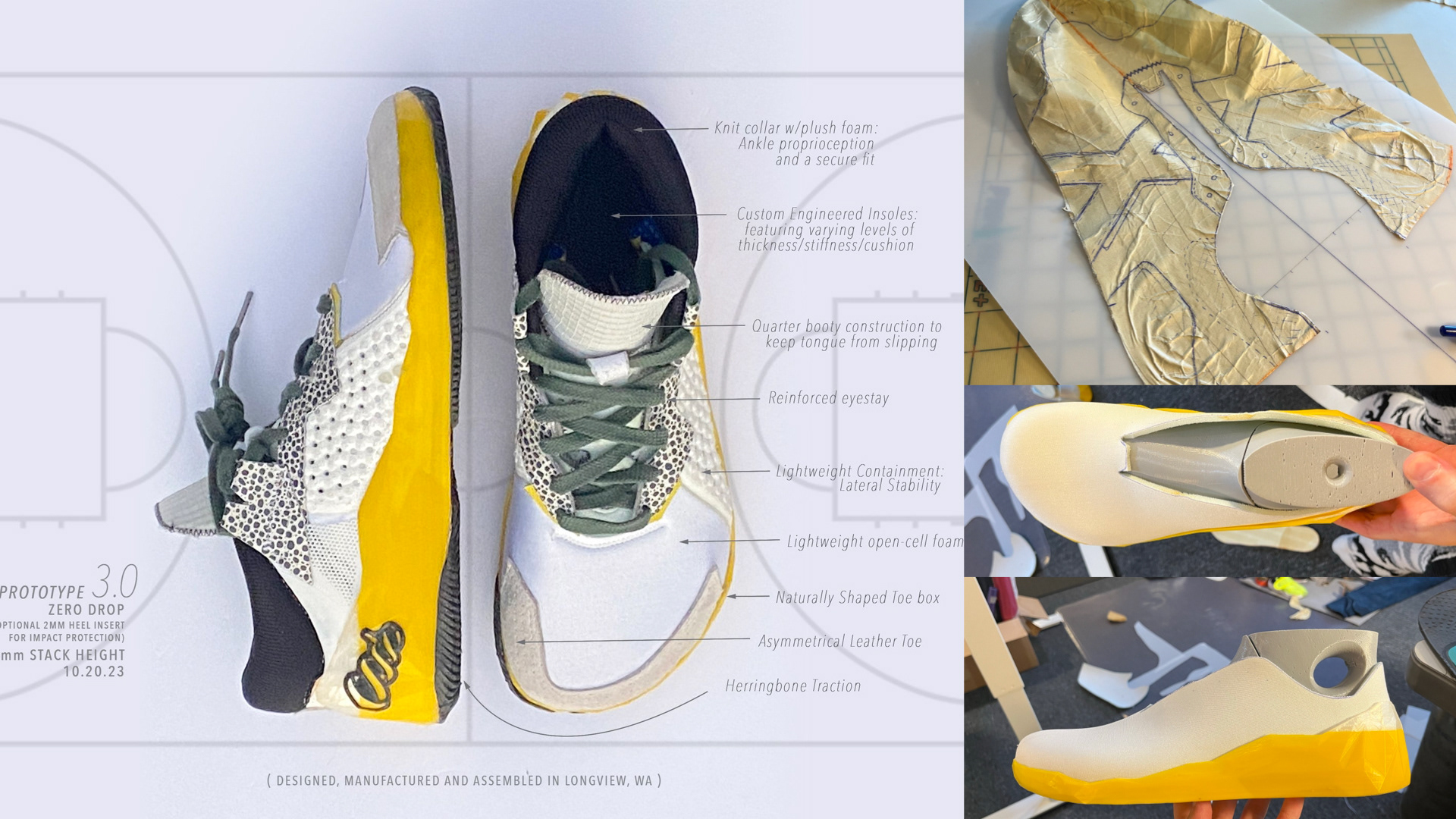